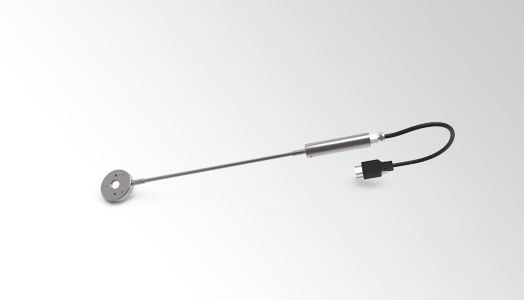
Irradiance Measurement of High-Power UV Light Sources (UV Curing)
High intensity UV radiation is present in a range of applications. For example, high power UV light sources are widely used for UV curing which presents a number of measurement challenges that need to be addressed.
UV curing is a photochemical process in which polymerization is initiated when photoinitiators, mixed within the material, absorb high energy UV [1]. Controlling the exposure of work pieces to UV energy (time and intensity) is essential in the curing processes widely used for coating, printing, adhesives, encapsulants and potting compounds. To monitor and adjust the UV energy, the irradiance needs to be measured as close as possible to the surface of the irradiated parts in order to represent the same exposure. Successful curing requires the correct dose of UV at the wavelengths appropriate for the particular material. Dose, measured in J/cm², is the product of UV intensity and time of exposure (W/cm² x seconds). UV intensity (irradiance) is measured by a UV radiometer in W/cm², but may also be displayed directly as a dose in J/cm². A suitable radiometer must also be able to withstand a high temperature environment or have the option to offer correction for temperature effects. Since such radiometers allow exceptional performance for such high intensity applications, the technology is also used for UV lithography applications (see App. 038 UV measuring devcies for mask aligners (lithography)).
There are two main types of UV source used to generate the needed high-intensity UV-irradiation:
1. High-Power Gas Discharge Lamps (e.g. medium pressure mercury lamps): These gas discharge lamps produce intense UV radiation by vaporizing the mercury into an extremely high-temperature plasma gas within a sealed quartz tube containing an inert gas mixture. The spectral composition can be modified to some degree by adding dopant metals such as iron or gallium. The emitted light is very well defined regarding its spectral peaks due to inner atomic transitions with defined energies. In addition to the UV radiation, gas discharge lamps also produce very high levels of IR radiation from the quartz envelope of the lamp, which may be either a help or a hindrance to the successful hardening of materials.
2. High-Power UV-LEDs (e.g. at 365 nm): In recent years, the trend has clearly been toward using high-power LEDs as light sources. With the most recent developments, they offer increasing UV outputs as well as the benefits of instant switch on and the resulting energy efficiency. Combined with the stability as well as life time advantages [2] LEDs are now at a very competitive level and will continue to improve. However, other topics such as the wavelength stability due to heating effects have to be considered. Since the absorption within the curing material is also closely related to the wavelength of the irradiation, deviations here can lead to changes of the curing process and its duration. Dose monitoring due to life time restrictions is of course still an important task. As mentioned, LEDs have significantly improved for UV applications, but aging is a significant effect [3].
An important fact: The output intensity of both gas discharge lamps and LEDs degrades over time. Therefore, to ensure the required dose is achieved, irradiance should be closely monitored. Using this information, process times can be adjusted to ensure the UV-curing process within the material is completed. Lamp replacement schedules can also be optimized based on such radiometric measurements.
Therefore, the selection of radiometers suitable for UV curing measurement employing high intensity gas discharge lamps as well as LEDs requires the following criteria to be met:
- Detector design for minimal ageing and drift when exposed to intense UV and heat radiation
- Cosine field-of-view detector (small f2) for high accuracy of irradiance measurements
- Flat-type detector enabling measurement plane to match that of the work piece surface
- Spectral responsivity of the detectors matched to the spectral sensitivity of the photo-initiators and the emission spectrum of the gas discharge lamp as well as LEDs
- Easy handling of the measuring device
- Protection of the user from the risk of intense UV and heat radiation
- Fast recalibration service and traceable calibration with options for ISO 17025 calibration and testing
Gigahertz-Optik offers different UV-curing measurement solutions which fulfill these requirements.
RCH-xxx Series: High Temperature Detector Series for Different Light Sources
For radiometric measurements in W/cm² and J/cm² (integral measurements), the RCH-xxx Series detector heads from Gigahertz Optik GmbH are most suitable. The innovative design of these proven measurement heads ensures that the sensitive photodetector is both thermally isolated and protected from the high UV levels present. With this concept, the RCH-Series has been meeting the high demands of radiation curing for many years with attractive price. Different versions for different light sources are available.
Cure-Met: An UV-Curing Disc
Gigahertz-Optik also transferred its knowledge for integral measurements into the Cure-Met, a UV-Curing disk. It offers the possibility to be placed on conveyor belts in order to run though larger curing setups. Here it continuously logs data in the internal storage to offer a local irradiance profile.
BTS256-UV: A superb Spectroradiometer for UV Curing Applications
A different solution is our BTS256-UV series of spectroradiometers. It offers not only an integral measurement, but also spectral details in addition. Particularly useful for LED-based light sources, this offers new opportunities to e.g. monitor the wavelength as well as to perform binning when selecting suitable LEDs.
Calibration
For any kind of radiometric irradiance measurement, calibration of the detector is a very critical parameter for the accuracy of the final measurement result. An underestimated topic for the integral measurements is the spectral mismatch and its correction to measure different light sources with high accuracy respectively low measurement uncertainty (see App. 020 Reduced Measurement Uncertainty for UV-A, UV-B and UV-C Radiometers ). In other words, a low calibration uncertainty which you can trust is important. In that respect we offer calibrations from our DAkkS ISO 17025 accredited calibration and testing laboratory. This means highest standards according to the ISO 17025 are applied to the processes to ensure reliability and traceability of our calibrations. All calibrations are directly traceable to the PTB, the German NMI, or comparable NMIs. Our calibration laboratory covers the wavelength range from 200 nm – 2500 nm and a variety of optical measurands.
References
[1] Photoinitiators for UV and visible curing of coatings: Mechanisms and properties
[2] Lifetime Analysis of Commercial 3 W UV-A LED
[3] Degradation of external quantum efficiency of AlGaN UV LEDs grown by hydride vapor phase epitaxy